The EHAWEDRY device energy conversion process focuses on low grade-waste heat and demands specific functional requirements in inputs such as hot dry air, sufficient air movement to facilitate the drying process, and the availability of water.
Although the technology has the potential to be applied across various scenarios by artificially creating the necessary input conditions, we identified potential scenarios where these input conditions are already existent to maximize cost-efficiency and practicality.
One of this potential scenarios is the textile industry.
The massive use of water in the textile industry
Water in both liquid and vapour forms and hot air play a critical role across a range of industries. In particular, the textile industry heavily relies on water and hot air for various stages of production, including processing, cleaning, and temperature control.
In the textile industry, drying processes are essential for reducing or eliminating water content from fabrics after wet treatments. Various drying techniques are utilized, including centrifugal extraction, pneumatic mangling, and evaporative drying. EHAWEDRY technology could be specifically applied to recover heat from the thermal evaporative drying process, where hot air is used to evaporate moisture from the fabric.
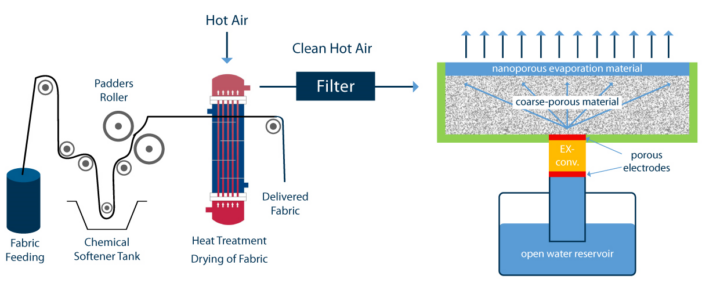
How the EHAWEDRY technology recovers heat
An example of a drying process is within the stenter machine, mainly used for drying fabrics. The process begins when the fabric is loaded into a trolley and then immersed in a solution bath. Through a series of rollers and tensioners, the fabric is guided to a weft straightener, ensuring even alignment before entering the drying chamber.
In this chamber, hot air is circulated across the fabric’s entire width on both sides, drying and stretching the material. The air temperature within the chamber typically ranges from 100°C to 180°C, depending on fabric requirements. While hot air is continuously recirculated within the system, a portion is removed and replaced by inflating fresh air to manage the level of humidity. The EHAWEDRY system could potentially recapture this hot air instead of exhausting it, reusing it back into the drying cycle.
Treatment of polluted wastewater
Water is the other fundamental element required for the EHAWEDRY operation. The textile industry employs huge amounts of water and in most cases discharges highly polluted wastewater. The Level of contamination varies with the process. For instance, wastewater from the scouring, dyeing, printing, and finishing stages is generally more polluted than the one used for washing and rinsing.
Typically, heavily contaminated wastewater is collected separately from less polluted streams.
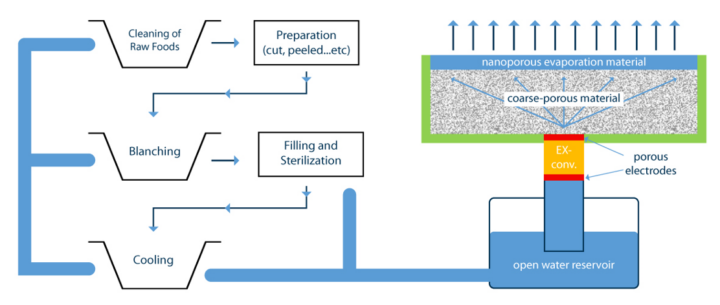
To minimize environmental impact, governments require textile factories to treat these effluents before discharge. The purified water can be certainly employed by the EHAWEDRY system for its wetting cycle, and the available heat could accelerate the subsequent device’s drying cycle.